Years of preparation
Getting access to the Pile Fuel Cladding Silo (PFCS), which was built with no thought to how it would be emptied, has been an incredible engineering challenge involving years of planning and preparation, hundreds of dedicated people and many millions of pounds of investment.
We’ve now made all the key modifications that are needed to get at the waste inside, so it’s ready to be emptied – both earlier and cheaper than forecast.
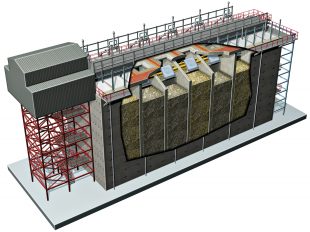
What … empty it all out?
The PFCS was built just after World War 2, based – rather bizarrely - on the design of American grain silos. It initially took the metallic casings, or ‘cladding’, shaved off spent nuclear fuel from the Windscale Reactors, and then later from Magnox power stations. The radioactive contents have lain undisturbed in the six tall concrete compartments for around 50 years. Back then, no-one even considered how, or indeed whether, it could be dismantled.
The approach we’re using is to install massive stainless steel doors on each compartment and cut openings in the wall behind them so a retrievals system can reach in and lift out the waste. We’ve built a reinforced concrete superstructure alongside the PFCS to manage all the work.
Just as 2017 came to an end, the final cuts were made on the sixth hole, so the last piece of concrete wall can be removed and the door lowered to enclose the radioactive contents until waste retrievals start in 2019. This completes the Retrieval Access Penetration (RAP) project.
Extra complication
That might sound straightforward but of course it’s hugely complicated and we’re working on a very congested part of Europe’s largest nuclear site which restricts what we can do. An extra complication is, in order to reduce the risk of fire, the atmosphere inside the PFCS is controlled by argon gas so this mustn’t escape during any of the procedures. It’s not toxic but can’t be breathed so all the work will be carried out remotely.
Retrieval equipment
Earlier in December 2017, we finished cutting up the 6 internal deflector plates. These are each about the size of a small car, made of steel, and were used to funnel waste as it was tipped in from above. We needed to remove the deflector plates so we could get our retrievals equipment in. Engineers used water jet-cutting equipment, preventing any sparks, and the pieces fell into the silo where they’ll eventually be removed along with the waste. This fully clears the way for the retrievals equipment to reach in through the newly cut holes.
Safely getting access to the waste inside the silo has been one of the most complex engineering challenges we’ve faced but it was a lovely Christmas present to complete the work 3 months early and under budget. We can now say the waste in the silo is ‘ready for retrieval’ for the first time in its life. And if progress continues at this pace, we could start retrievals before the 2020 date that is itself an improvement on the earlier 2022 date.
Team effort
It’s been a massive team effort with our main contractor partner Bechtel Cavendish Nuclear Solutions and suppliers such as Babcock Marine Technology, James Fisher Nuclear and Shepley Engineers.
The focus is now on manufacturing and installing all the equipment which will reach in, grab the waste and allow it to be safely exported for safer storage.
We’ve also changed the original plan for this work and, instead of using a robotic arm, the team will use a more standard and cost-effective extending boom crane.
Overall, the timescale for the start of retrievals has been cut by around 3 years, reducing costs to the taxpayer by around £250 million.
What happens next?
Now that we’ve completed installation of the doors, removal of the deflector plates and cutting of the holes, all the equipment used for those tasks can be cleared out of the way so we can install the waste retrieval modules during 2018.
Manufacturing of the equipment is already well under way, mostly by specialist suppliers at Rosyth in Scotland. It will then be brought to Sellafield site to be assembled on the ‘retrievals superstructure’.
At the foot of the superstructure, meanwhile, all the equipment and building modifications will be installed that will allow waste to be exported out from the PFCS. The waste will be received at the Box Encapsulation Plant Product Store Direct Import Facility – or BEPPS DIF for short.
Of course, the retrieved waste has to be contained somewhere, so we’ll also be ramping up production of the 3m³ boxes which will store it.
Read more about the NDA’s plan for the next few years
We’d like to hear your views on our work to decommission all our 17 UK nuclear sites, as outlined in our latest Business Plan.
Comment on our latest Business Plan, for 2018-2021, before 4 February
1 comment
Comment by Peter Whitehead posted on
I remember working on the concepts for decommissioning the Silo in the early 1990’s.
Then it was a different strategy to assess if the waste could be removed without dismantling the deflector plates.
I remember hunting down the original 1950’s drawings from Microfiche and modelling the silo in IGRIP.
I came up with a weird and wonderful machine that mounted on the existing service tunnel crane beams.
The machine had a water glycol actuated telescopic cylinder mounted on a gimbal attached to a slewing ring.
Off the end projected a stainless steel petal grab to retrieve the swarf.
Fascinating work although a very slow process for obvious reasons.
Looks like a whole new ball game now and I am sure the team involved are doing a tremendous (very underrated) job.
Hope it all continues to go according to plan.